*** Open Source Integrators - OCA Platinum Sponsor Blog Post ***
As a solution consultant specializing in MRP implementations, I see many manufacturing companies grappling with a common challenge – evolving their IT systems to keep up with the advancements they need to stay competitive. In each of these scenarios, the success of manufacturing businesses hinges on their ability to adapt to technological advancements and optimize operational efficiency, at scale, without massive capital outlay or unnecessary operational downtime. One of the key challenges faced by these manufacturers is effectively managing and automating their business processes to increase throughput, without necessarily adding more resource hours. From production to supply chain management, finding the right balance between manual labor and automation is essential for sustainable growth and profitability.
The Struggle of Traditional Approaches
In the past, most manufacturing operations relied heavily on manual labor and simple processes. While this approach may have been sufficient in the past, it is no longer a viable solution for those who wish to stay competitive in today's fast-paced manufacturing environment. Manual processes are prone to errors, inefficiencies, and increased production costs. They often lack the agility needed to respond to changing market demands and fluctuations in supply chain dynamics.
The Imperative of Automation
Automation holds the key to addressing many of the challenges faced by manufacturers. By leveraging cutting-edge technologies such as robotics, artificial intelligence (AI), and advanced analytics, businesses can streamline their operations, by using modern systems like Advanced Planning and Scheduling to enhance productivity, and drive innovation. Automation not only reduces labor costs but also improves accuracy, speed, and reliability across the entire production process.
Harnessing Advanced Manufacturing Technologies
Manufacturers can optimize their operations by leveraging advanced technologies such as the Internet of Things (IoT), big data analytics, and predictive maintenance. IoT sensors embedded in machinery and equipment enable real-time monitoring of production processes, allowing for proactive maintenance and minimizing downtime. Regardless of scale, achieving long-term visibility of operational efficiency and uncovering optimization opportunities as you grow can be done without the need for new analytics technologies. Existing big data analytics tools provide actionable insights into production trends, customer preferences, and market demand. This facilitates informed decision-making and strategic planning, enhancing efficiency, maximizing resource utilization, and ensuring your products and services remain relevant and competitive in a dynamic market.
The Role of Cloud-Based Solutions
On-premises solutions are often risky and expensive due to the high upfront costs, complex maintenance requirements, and potential for downtime. In contrast, cloud solutions are more cost-effective, offering flexible scalability and reduced risk. They allow businesses to outsource some or all of their technical deployment and management needs, simplifying operations and lowering overall costs—with a company like OSI ready to help every step of the way.
Cloud based solutions such as Odoo can be an indispensable tool for managing and automating manufacturing processes. From enterprise resource planning (ERP) systems to supply chain management (SCM) platforms, cloud-based solutions offer scalability, flexibility, and accessibility. By centralizing data and applications in the cloud, manufacturers can streamline collaboration, enhance data security, and facilitate seamless integration with third-party systems and partners. One of the biggest benefits of a cloud-based ERP solution is overall reduced costs, which begins at implementation.
Overcoming Challenges and Driving Success
While the benefits of managing and automating manufacturing processes are undeniable, implementation challenges may arise. Resistance to change, lack of skilled workforce, and upfront investment costs are some of the common obstacles faced by manufacturers. However, by fostering a culture of innovation, investing in employee training, and partnering with technology providers, businesses can overcome these challenges and unlock the full potential of automation.
Navigating ERP Implementation Challenges
At OSI, our implementation process revolves around four key principles: Analyzing, Optimizing, Automating, and Transitioning. We begin by deeply understanding your business needs, optimize processes for efficiency, automate repetitive tasks, and ensure a seamless transition to your new system. This approach goes beyond standard implementation, aiming to elevate your company to excellence.
Read more about OSI’s implementation process methodology here to see what makes our approach unique (and efficient).
Conclusion
In conclusion, effectively managing and automating manufacturing business processes is critical for staying competitive in today's market. By embracing automation, harnessing advanced technologies, and leveraging cloud-based solutions, manufacturers can streamline operations, improve productivity, and drive sustainable growth. While the journey towards automation may be daunting, the rewards are well worth the investment. With the right strategy and mindset, manufacturing businesses can thrive in the digital age and lead the way towards a more efficient and agile future.
Challenges that you might be facing in manufacturing businesses is to adapt to rapidly evolving technological landscapes.
Learn more about how OSI can help you in these challenges around manufacturing and by working with our experts, we can find the best solution to fit your needs.
OCA Platinum Sponsor
Sponsor Blog Post
About the Author
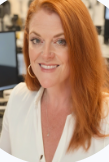
Melody Fetterly
Sr Solution Consultant, Open Source Integrators
Melody Fetterly, a manufacturing software expert and dedicated mom of two, resides in Queen Creek, Arizona. She began her career in a small factory, where she gained comprehensive experience by working in every role, from customer service to shipping. This diverse background propelled her into the manufacturing industry, where she has made significant contributions by implementing various ERP solutions across multiple sectors.
Melody excels in planning and operational improvements, having led numerous successful initiatives to streamline processes and achieve strategic goals. Her expertise in policy development and staff management consistently enhances team morale and productivity, making her an invaluable asset in any organizational setting. Melody is passionate about empowering women and inspiring the next generation of process improvement professionals, continually fostering an environment of growth and development.
The views and opinions expressed are those of the author and do not necessarily reflect the official policy or position of the Odoo Community Association. Any content provided by our sponsors or authors are of their opinion and are not intended to malign any religion, ethnic group, club, organization, company, individual or anyone or anything.